
Y-coat's Merits in Different Processes
Here we introduce Y-coat effects and merits under various cases, and recommend the most suitable coating types based on our rich knowledge and experience.
Please contact us if you need more details.

Theme |
Longer and More Stable Life for Punch Die
Name: Punch Die |
Die Material: Super Hard V30 Equivalent |
Work Piece: SCM |
Size: Φ20×25mm |
Surface:CVD-TiCN |
|
|
Problem |
・When processing was done with CVD-TiCN, the life was not stable (100~150,000 shots) due to damage to the punch itself. |
Countermeasure |
・Changed to Y-coat Type CN ( TiCN ) using ion-plating method, which resulted in constant and stable compressive stress to plated film. |
Result |
・Usable life became constant, leading to reduction in total cost.
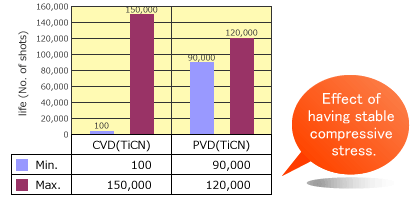
|