Environmental targets
Environmental Goals of TL Division
Actual value in 2022 | Target value for 2025 | Target value for 2030 | |
---|---|---|---|
Plant CO2 | 1,200t/year | Reduce emissions by 10% | Reduce emissions by 15% |
Electric energy | Electricity consumption 2,523,000kwh |
2% reduction in electricity usage charges (Excludes solar power generation) |
5% reduction in electricity usage charges (Excludes solar power generation) |
CO2 emissions from mold making | 11,600t/year | Improved mold life by 10% (Reduce mold production quantity by 10%) |
Improved mold life by 30% (Reduce mold production quantity by 30%) |
Mixed waste (paper waste, cardboard, vinyl) |
1.1t/year | 50% reuse (Total:paper waste, cardboard, vinyl) |
10% reuse (Total:paper waste, cardboard, vinyl) |
Waste liquids and oil (alkali waste liquids and draining agents) |
Waste alkali : 91.2t/year Waste oil : 12.0t/year |
Reduce amount of waste by 40% (Total:waste alkali, waste oil) |
Reduce amount of waste by 80% (Total:waste alkali, waste oil) |
Waste metals (scrap iron, stainless steel) |
3.4t/year | Reduce amount of waste by 20% (Total:scrap iron, stainless steel) |
Reduce amount of waste by 40% (Total:scrap iron, stainless steel) |
Aiming for Environmentally Sound Coatings
The TL Division will address events that have an environmental impact in each process, and the entire industry will work together to achieve environmentally sound coatings, from small improvements to major improvements.
- Electricity & Plant CO2 Reduction Activities
The coating process consumes a great deal of electricity to heat the molds.
We are working to reduce power consumption by having our customers make reservations in advance to ensure waste-free and highly efficient processing.
We also aim to reduce electricity consumption by 5% and CO2 emissions by 15% through the introduction of solar power and the cumulative effect of small improvements.
- CO2 reduction activities through mold making
Considering the life cycle of a mold, CO2 emissions account for 70% of the total emissions before the coating process (from steelmaking to mold fabrication). In order to reduce CO2 emissions during mold fabrication, we aim to achieve a 30% increase in mold life (30% reduction in mold fabrication) through coating.
- Mixed waste reduction activities
We use many packing materials to protect our customers’ valuable molds from shocks during transportation.
We aim to reuse 10% of the packaging materials used at the time of arrival.
- Activities to reduce liquid waste and waste oil
To achieve a coating process with high adhesion, the mold surfaces are cleaned by various methods.
We aim to reduce the amount of waste cleaning solution by 80% by extracting pure water from the waste solution and promoting its reuse.
- Waste metal
In order to meet customer requirements, we use various methods to fix molds at the time of film deposition, and the fixing materials are disposed of each time. We will continue to devise and improve fixing methods to improve quality and filling volume, and aim to reduce metal waste by 40%.
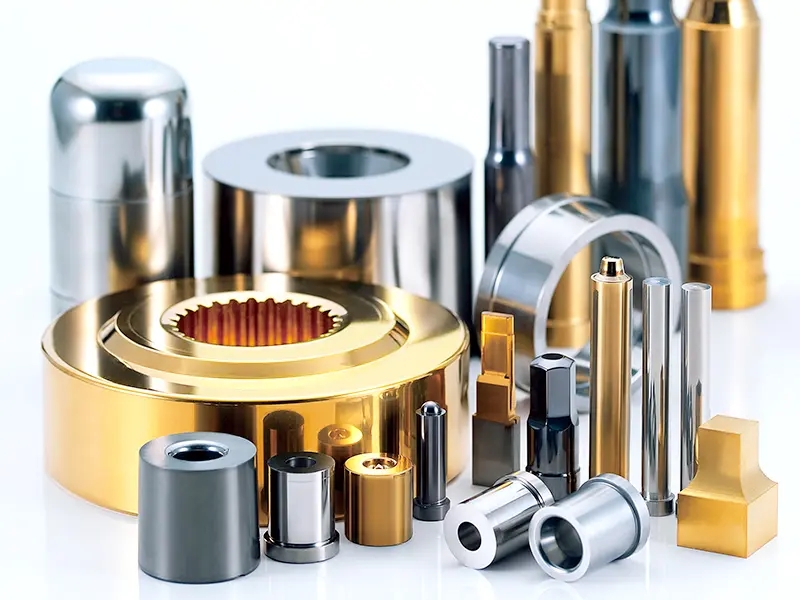